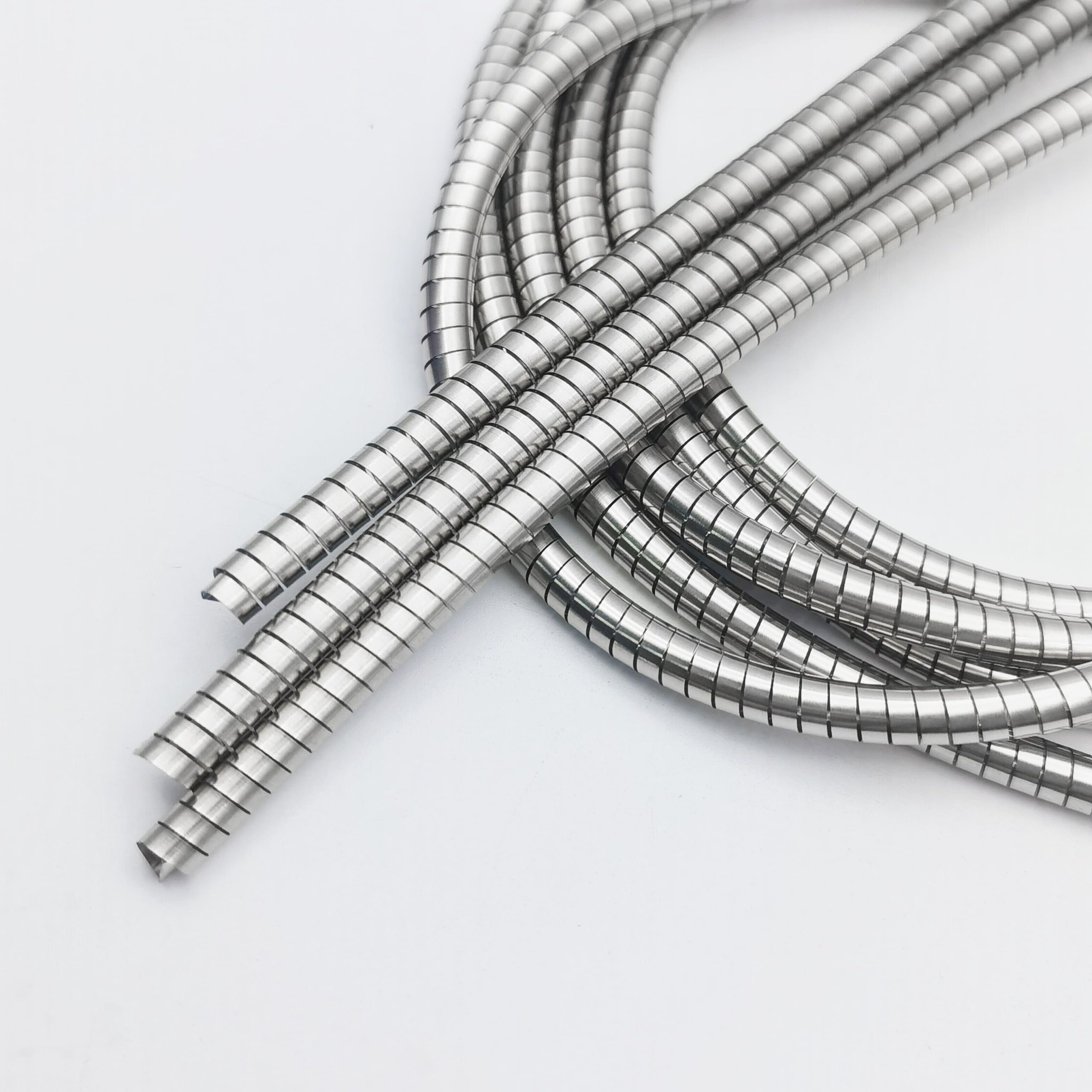
Helical springs (O-type springs)
Helical springs (O-type springs) are indispensable mechanical components that convert mechanical energy into elastic potential energy through controlled deformation. Their applications span industries such as automotive, aerospace, medical devices, and energy systems.
1. Physical and Mechanical Principles
1.1 Elasticity and Hooke’s Law
Helical springs operate under Hooke’s Law (F=k⋅xF=k⋅x), where stiffness (kk) is determined by:
- G: Shear modulus (e.g., 77 GPa for stainless steel).
- d: Wire diameter.
- D: Mean coil diameter.
- N: Number of active coils.
Dynamic Response:
Natural frequency (fnfn) must exceed operational frequencies to avoid resonance:
where m is the effective mass of the Helical springs.
1.2 Stress Analysis and Failure Modes
- Kw: Wahl correction factor
- Fatigue Failure: Governed by S-N curves; high-cycle fatigue (>10⁴ cycles) requires stress below the endurance limit.
2. Material Science and Engineering Selection
- Carbon Steel (SAE 1070):
- Microstructure: Tempered martensite after quenching (hardness HRC 45–50).
- Applications: Low-cost industrial springs (e.g., agricultural machinery).
- Stainless Steel (316L):
- Molybdenum-enhanced corrosion resistance; cold-worked for strain hardening.
- Used in marine environments and chemical processing.
- High-Temperature Alloys (Inconel 718):
- γ” phase (Ni₃Nb) precipitation hardening; serviceable up to 650°C.
- Critical in jet engine combustor springs.
2.2 Composite and Smart Materials
- Carbon Fiber-Reinforced Polymer (CFRP):
- Specific stiffness 5× higher than steel; used in Formula 1 suspension systems.
- Limitations: Brittle fracture under impact loading.
- Shape Memory Alloys (NiTi):
- Superelasticity (8% recoverable strain); ideal for minimally invasive surgical tools.
- Phase transformation temperatures (AfAf) tailored via alloying (e.g., NiTi-Cu).
3. Advanced Manufacturing Techniques
3.1 Precision Coiling Technologies
- CNC Spring Coiling Machines:
- Multi-axis control for variable pitch and conical springs (tolerance ±0.01 mm).
- Example: WAFIOS FK 8.0 series for medical microsprings (wire diameter 0.1–2.0 mm).
- Hot Coiling Process:
- For wires >12 mm: Heat to 850–950°C (austenitizing), coil, then oil quench.
- Post-treatment: Tempering at 400–500°C to relieve residual stresses.
3.2 Surface Engineering
- Shot Peening:
- Almen intensity 0.3–0.6 mmA; induces compressive stress (-200 to -800 MPa).
- Extends fatigue life by 3–5× in automotive valve springs.
- PVD Coatings (TiN/CrN):
- Reduces friction coefficient to 0.1–0.2; used in hydraulic seal springs.
3.3 Quality Assurance
- Eddy Current Testing: Detects surface cracks (>0.1 mm depth) at 100% production rate.
- X-ray CT Scanning: Identifies internal voids/inclusions (resolution <10 μm) in aerospace-grade springs.
4. Industrial Applications and Case Studies
4.1 Automotive Industry
- Electric Vehicle (EV) Battery Modules:
- Challenge: Vibration (20–200 Hz) and electrolyte corrosion (LiPF₆).
- Solution: 316L springs with PTFE coating; preload ≥200 N.
- Brake-by-Wire Systems:
- Microsprings (Ø0.3 mm) in solenoid valves; cycle life >10⁷; response time <5 ms.
4.2 Medical Devices
- Bioabsorbable Vascular Stents:
- Material: Mg-Zn-Ca alloy; degradation rate 0.2–0.5 mm/year.
- Clinical outcome: Full absorption within 12–18 months post-implantation.
- Chirurgische Robotik:
- Miniature springs (Ø0.5 mm) in forceps joints; precision ±0.1 N force control.
4.3 Energy and Heavy Industry
- Nuclear Reactor Control Rod Springs:
- Material: Inconel 718; neutron irradiation resistance (<1% swelling at 10²⁰ n/cm²).
- Design: Redundant spring stacks for fail-safe operation.
- Offshore Oil Drilling:
- Blowout Preventer (BOP) springs: Inconel 625 + PEEK encapsulation; API 16A certified.
5. Computational Design and Simulation
5.1 Finite Element Analysis (FEA)
- Nonlinear Static Analysis:
- Simulates plastic deformation (e.g., Chaboche model) in overload scenarios.
- Case: Oil valve spring stress must remain <80% of σ_y (1,100 MPa for Inconel 718).
- Fatigue Life Prediction:
- Manson-Coffin equation for low-cycle fatigue:
- Software: ANSYS nCode DesignLife for probabilistic fatigue analysis.
5.2 Multiphysics Coupling
- Thermal-Mechanical Analysis:
- Temperature-dependent EE (e.g., 316L’s E drops 30% at 600°C).
- Case: Turbocharger wastegate springs in exhaust gas environments (700°C).
- Fluid-Structure Interaction (FSI):
- Models fluid pulsation effects on hydraulic seal springs; damping ratio optimized to <0.1.
5.3 AI-Driven Design Optimization
- Topology Optimization:
- Altair OptiStruct reduces mass by 20–40% while maintaining kk (e.g., wind turbine pitch springs).
- Generative Design:
- Neural networks predict optimal dd, DD, and NN for custom load-displacement curves.
6. Intelligent Spring Systems
6.1 Embedded Sensor Networks
- Fiber Bragg Grating (FBG) Sensors:
- Strain resolution ±1 με; embedded in bridge seismic isolation springs.
- Piezoelectric Energy Harvesting:
- Converts vibration to electricity (10 mW); powers wireless sensors in railway track springs.
6.2 Active Control Mechanisms
- Magnetorheological (MR) Fluid Springs:
- Adjustable stiffness (10× range); response time <20 ms for vehicle semi-active suspensions.
- Shape Memory Alloy Actuators:
- SMA springs contract upon Joule heating; used in Mars rover deployable solar arrays (force 500 N/mm²).
6.3 Digital Twin Integration
- Spring-Twin Platform:
- Combines IoT sensor data, material aging models, and load history for real-time health monitoring.
- Machine Learning for Predictive Maintenance:
- LSTM networks analyze vibration spectra to forecast residual life (accuracy >85%).
7. Sustainable Technologies
7.1 Eco-Friendly Materials
- Polylactic Acid (PLA) Springs:
- Biodegradable; tensile strength 50 MPa; used in disposable laparoscopic tools.
- Hydrogen Embrittlement Mitigation:
- Vacuum degassing reduces H₂ content to <0.1 ppm in AISI 4340 high-strength springs.
7.2 Remanufacturing and Repair
- Laser Cladding:
- CoCr alloy deposition (0.2 mm layers); hardness restored to HRC 55.
- Cold Spray Additive Repair:
- Al-Si coatings on cracked springs; post-heat treatment recovers 90% fatigue life.
7.3 Recycling and Circular Economy
- Laser-Induced Breakdown Spectroscopy (LIBS):
- Material identification accuracy >99%; enables alloy-specific sorting.
- Arc Furnace Remelting:
- Recycled spring steel reduces CO₂ emissions by 1.8 tons per ton vs. virgin material.
8. Future Technological Frontiers
8.1 Extreme Environment Adaptability
- Oxide Dispersion Strengthened (ODS) Alloys:
- MA754 (Ni-20Cr-0.5Y₂O₃) for 1,000°C applications (e.g., hypersonic vehicle engines).
- Radiation-Shielding Coatings:
- Boron-doped SiC coatings for lunar habitat springs (neutron absorption 5× higher).
8.2 Micro/Nano-Scale Fabrication
- MEMS Springs:
- Photolithography + electroplating for 10 μm-wide springs; force resolution 1 pN in AFM probes.
- Carbon Nanotube (CNT) Springs:
- CVD-grown CNT bundles with 1 TPa·g⁻¹·cm³ specific modulus; nanorobotic joint drivers.
8.3 Cross-Disciplinary Innovations
- Bio-Inspired Springs:
- Resilin protein-mimetic polymers for 90% energy recovery (e.g., robotic jumping mechanisms).
- Quantum Mechanical Systems:
- Superconducting NbTi springs for quantum computing cryogenic stages (0.1 nm positioning accuracy).
Schlussfolgerung
Schraubenfedern are transitioning from passive components to intelligent, adaptive systems through advancements in materials science, digital twins, and sustainable manufacturing. Future challenges lie in conquering extreme environments, enabling nanotechnology-scale applications, and achieving full lifecycle circularity. As industries embrace Industry 4.0 and net-zero goals, helical springs will remain pivotal in merging mechanical reliability with ecological stewardship.